Density of Bentonite Slurry
1. Classification and Performance of slurry
1.1 Classification
Bentonite, also known as bentonite rock, is a clay rock featuring high-percentage of montmorillonite, which often contains a small amount of illite, kaolinite, zeolite, feldspar, calcite, etc. Bentonite can be categorized into three types: sodium-based bentonite (alkaline soil), calcium-based bentonite (alkaline soil) and natural bleaching earth (acidic soil). Among them, calcium-based bentonite could be categorized into calcium-sodium-based and calcium-magnesium-based bentonites, too.
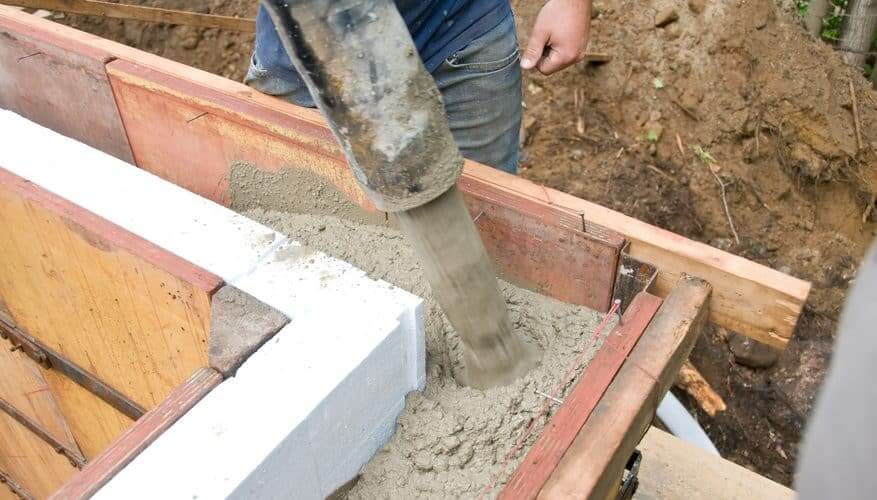
1.2 Performance
1) Physical Properties
Bentonite is white and light yellow in natural while it also appears in light gray, light green pink, brown red, black, etc. Bentonite vary in stiffness due to their physical properties.
2) Chemical Composition
The main chemical components of bentonite are silicon dioxide (SiO2), aluminum oxide (Al2O3) and water (H2O). The content of iron oxide and magnesium oxide is also high sometimes, and calcium, sodium, potassium are often present in bentonite in different contents. The content of Na2O and CaO in bentonite makes a difference on the physical and chemical properties, and even process technology.
3) Physical & Chemical Properties
Bentonite outstands in its optimal hygroscopicity, namely expansion after water absorption. The expansion number involving water absorption reaches high to 30 times. It can be dispersed in water to form a viscous, thixotropic, and lubricate colloidal suspension. It turns malleable and adhesive after mixed with of fine debris such as water, slurry or sand. It’s able to absorb various gases, liquids, and organic substances, and the maximum adsorption capacity can reach 5 times its weight. The surface-active acid bleaching earth can adsorb colored substances.
The physical and chemical properties of bentonite mainly depend on the type and content of montmorillonite it contains. In general, sodium-based bentonite has superior physical and chemical properties and technology performance than calcium-based or magnesium-based bentonite.
2. Continuous Measurement of Bentonite Slurry
The Lonnmeter inline bentonite slurry density meter is an online pulp density meter frequently used in industrial processes. The density of slurry refers to the ratio of the weight of slurry to the weight of a specified volume of water. The size of the slurry density measured on-site depends on the total weight of the slurry and drill cuttings in the slurry. The weight of admixtures should be included too if any.
3. Application of Slurry under Different Geological Conditions
It’s difficult to drill a hole in sander, gravel, pebbles layers and broken zones for junior bonding properties among particles. The key to the problem lies in increasing bonding force among particles, and takes slurry as a protective barrier in such strata.
3.1 Effect of Slurry Density on Drilling Speed
The drilling speed decreases with increasing slurry density. The drilling speed decreases significantly , especially when the slurry density is greater than 1.06-1.10 g/cm3. The higher the viscosity of the slurry is, the lower the drilling speed.
3.2 Effect of Sand Content in Slurry on Drilling
The content of rock debris in the slurry poses risks on drilling, resulting in improper purified holes and subsequent stuck. In addition, it may cause suction and pressure excitement, resulting in leakage or well collapse. The sand content is high and the sediment in the hole is thick. It causes the hole wall to collapse due to hydration, and it is easy to cause slurry skin to fall off and cause accidents in the hole. At the same time, the high sediment content causes great wear on pipes, drill bits, water pump cylinder sleeves, and piston rods, and their service life is short. Therefore, under the premise of ensuring the balance of formation pressure, the slurry density and sand content should be reduced as much as possible.
3.3 Slurry Density in Soft Soil
In soft soil layers, if the slurry density is too low or the drilling speed is too fast, it will lead to hole collapse. It is usually better to keep the slurry density at 1.25g/cm3 in this soil layer.
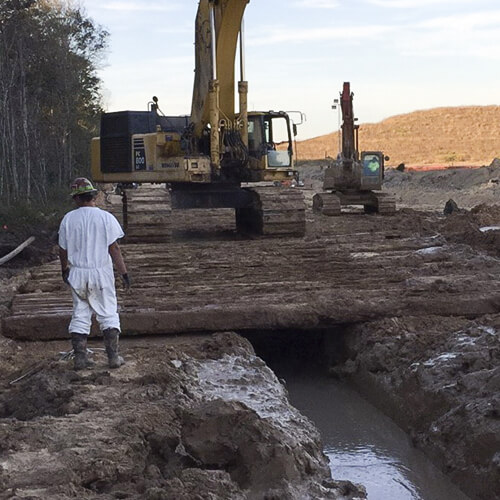
4. Common Slurry Formulas
There are many types of slurry in engineering, but they can be classified into the following types according to their chemical composition. The proportioning method is as follows:
4.1 Na-Cmc (Sodium Carboxymethyl Cellulose) Slurry
This slurry is the most common viscosity-enhancing slurry, and Na-CMC plays a role in further viscosity enhancement and water loss reduction. The formula is: 150-200g of high-quality slurry clay, 1000ml of water, 5-10Kg of soda ash, and about 6kg of Na-CMC. slurry properties are: density 1.07-1.1 g/cm3, viscosity 25-35s, water loss less than 12ml/30min, pH value about 9.5.
4.2 Iron Chromium Salt-Na-Cmc Slurry
This slurry has strong viscosity enhancement and stability, and iron chromium salt plays a role in preventing flocculation (dilution). The formula is: 200g clay, 1000ml water, about 20% addition of pure alkali solution at 50% concentration, 0.5% addition of ferrochromium salt solution at 20% concentration, and 0.1% Na-CMC. The slurry properties are: density 1.10 g/cm3, viscosity 25s, water loss 12ml/30min, pH 9.
4.3 Lignin Sulfonate Slurry
Lignin sulfonate is derived from sulfite pulp waste liquid and is generally used in combination with coal alkali agent to solve the anti-flocculation and water loss of slurry on the basis of viscosity increase. The formula is 100-200kg clay, 30-40kg sulfite pulp waste liquid, 10-20kg coal alkali agent, 5-10kg NaOH, 5-10kg defoamer, and 900-1000L water for 1m3 slurry. The slurry properties are: density 1.06-1.20 g/cm3, funnel viscosity 18-40s, water loss 5-10ml/30min, and 0.1-0.3kg Na-CMC can be added during drilling to further reduce water loss.
4.4 Humic Acid Slurry
Humic acid slurry uses coal alkali agent or sodium humate as a stabilizer. It can be used in conjunction with other treatment agents such as Na-CMC. The formula for preparing humic acid slurry is to add 150-200kg coal alkali agent (dry weight), 3-5kg Na2CO3, and 900-1000L water to 1m3 of slurry. slurry properties: density 1.03-1.20 g/cm3, water loss 4-10ml/30min, pH 9.
Post time: Feb-12-2025