Mining and mineral processing is the critical industry in global economy for the tremendous economic output value. The importance of efficiency and accuracy grows increasingly as more difficulties in extraction and stringent regulations come into effect.
Continuous slurry density measurement gained its position and positive reviews even among various technological breakthroughs that have shaped these industries. The article concentrates on various applications of slurry density measurement and corresponding instruments -- slurry density meters. Emphasize the significance in optimizing efficiency and saving unnecessary operational cost.
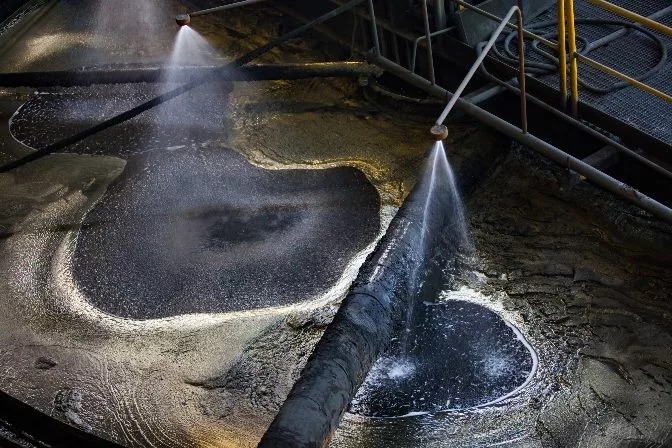
Efficient Separation of Valuable Minerals
The efficient separation of valuable minerals from tailing waste requires precision monitor of slurry density, which guarantees the correct concentration of materials in processing plants. No matter processing of ores or minerals, consistency and concentration make a difference in separation efficiency. Traditional manual density measurement causes human errors and postpone of real-time decision-making.
Nevertheless, process automation and continuous density measurement is badly needed in plants for optimization against breakthroughs in technology. One of the key advantages of inline density meters is their ability to optimize energy consumption in milling operations.
Maintaining an ideal slurry density reduces the wear and tear on grinding equipment, extending its operational life. Accurate density control minimizes inefficiencies in the grinding process, which directly translates to reduced power consumption and lower operational expenses.
Additionally, these systems can integrate seamlessly with plant automation setups, enabling proactive maintenance schedules. By avoiding unnecessary strain on equipment and ensuring consistent operating conditions, operators can achieve both sustainability goals and significant cost savings.
Improve Recovery Rates & Yield Optimization
The primary task in mining is to optimize the recovery rates in a more cost-effective way. For optimization in above aspects, the first steps are reaching this goal to prioritize. It helps operators maintain optimal process conditions, resulting in improved yield and resource utilization.
For instance, in flotation processes, the balance of slurry density is crucial. If the slurry is too dense, it hampers the dispersion of air bubbles, which are critical for separating minerals. Conversely, overly diluted slurry increases reagent consumption, driving up costs and reducing process efficiency. By fine-tuning slurry density, plants can significantly enhance mineral recovery while minimizing waste.
Modern inline density measurement systems continuously monitor slurry characteristics and provide real-time data. These systems allow for instant adjustments, ensuring the processing plant operates within the desired parameters. Furthermore, integration with broader plant control systems enables centralized management of all operational variables, offering both precision and efficiency gains.
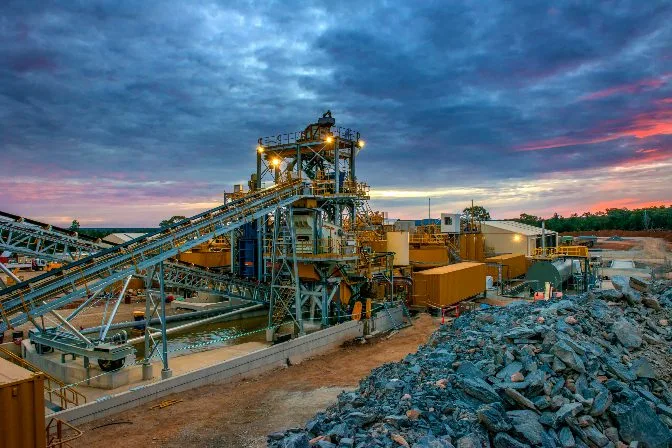
Environmental Compliance and Resource Conservation
In addition to operational efficiency, slurry density measurement plays a critical role in environmental and regulatory compliance. Managing tailings, the waste byproduct of mineral processing, is a major challenge in mining. Precise density measurements help optimize the handling and disposal of tailings, reducing the risk of environmental hazards such as seepage or dam failures.
Accurate data also aids in water conservation, a vital concern in water-scarce regions. By controlling slurry density, plants can recover and recycle water more effectively from waste streams, significantly reducing their overall water footprint. This not only supports sustainable practices but also ensures compliance with stringent regulatory requirements.
Cutting Costs and Boosting Profitability
Accurate density monitoring leads to tangible economic advantages. First, it optimizes the use of reagents during separation processes, significantly reducing chemical costs. Additionally, proper slurry density ensures that grinding and milling operations run at peak efficiency, cutting energy consumption and minimizing wear on equipment. Over time, these savings accumulate, lowering maintenance expenses and extending equipment lifespan.
Furthermore, higher recovery rates achieved through precise slurry control translate directly into increased revenue. Processing plants extract more valuable material from the same ore volume, maximizing profitability while generating less waste—a win-win scenario for both operators and the environment.
Advances in Technology: Enhancing Accuracy and Usability
Technological innovation is transforming slurry density measurement. Non-contact systems using ultrasonic, microwave, or gamma radiation now dominate the market due to their durability and accuracy in harsh mining environments. These systems are designed to withstand extreme conditions like high pressure, temperature, and abrasive slurries, ensuring reliable performance with minimal maintenance.
The integration of advanced data analytics and machine learning has further improved operational insights. Predictive models analyze real-time and historical data to forecast process trends, enabling proactive adjustments. Portable density meters have also emerged, offering flexibility for remote or field-based measurements, ensuring that even isolated locations can benefit from accurate density monitoring.
Conclusion
Slurry density measurement is an indispensable aspect of mining and mineral processing, driving efficiency, profitability, and sustainability. By optimizing operational parameters, reducing environmental impact, and lowering costs, these systems ensure long-term competitiveness. As technology continues to evolve, the industry can expect further advancements, enabling even more refined control over processes and resources.
Post time: Dec-27-2024