The dense liquid is a high-density liquid used to separate the desired ore from rocks and gangue minerals. It exhibits good chemical stability, resisting decomposition, oxidation, and other chemical reactions, to maintain its density and separation performance in general. The dense liquid is typically an aqueous solution of various soluble high-density salts (e.g., zinc chloride solution) or high-density organic liquids (e.g., tribromomethane, carbon tetrachloride).
The primary application of dense liquid is in dense medium coal separation, where it separates materials of different densities through buoyancy. Materials with a density greater than that of the dense liquid sink, while those with a lower density float on the liquid's surface, enabling the separation of coal and gangue.
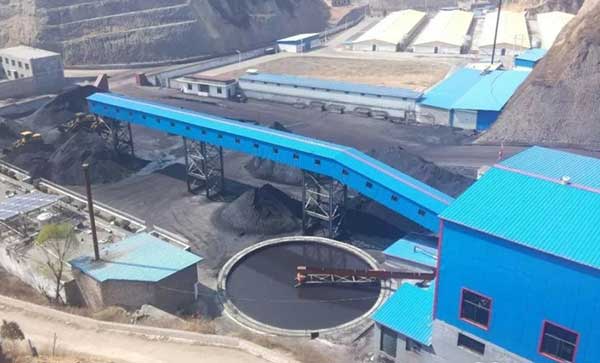
Benefits of Dense liquid Density Monitoring
The density of the dense liquid is a critical factor in the separation of coal and gangue. If the density of the dense liquid is unstable and fluctuates significantly, the actual separation density may deviate from the optimal value, leading to inaccurate separation of coal and gangue. For instance, if the density is too low, some gangue may be incorrectly selected as clean coal, increasing the ash content in the clean coal; if the density is too high, some coal may be discarded as gangue, reducing the recovery rate of clean coal.
Maintaining a stable dense liquid density helps ensure consistent quality of clean coal products. Density fluctuations can lead to significant changes in quality indicators such as ash and sulfur content in the clean coal, adversely affecting the product's market competitiveness.
Operators can promptly adjust the composition and circulation of the dense liquid, ensuring the washing process remains in optimal condition. This reduces repeated washing and equipment idling caused by unsuitable density, thereby improving production efficiency, reducing energy consumption, and lowering production costs.
Excessively high or low density of the heavy liquid can cause varying degrees of damage to the washing equipment. For instance, excessively high density increases the load on the equipment, leading to accelerated wear and tear and even potential equipment failures; low density may compromise the separation effectiveness, reducing the equipment’s operational efficiency.
By measuring and promptly adjusting the density of the heavy liquid, the normal operation of the equipment can be ensured, thereby extending its service life.
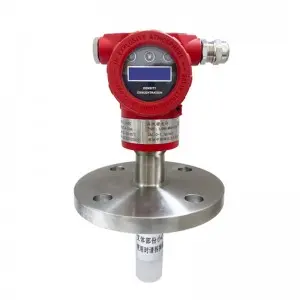
Recommended Inline Flow Density Meter
The inline process density meter utilizers the acoustic frequency of a signal source to excite a metal tuning fork, causing it to vibrate freely at its natural frequency. This frequency corresponds to the density of the dense liquid in contact with the tuning fork. By analyzing the frequency, the density is measured, and temperature compensation is applied to eliminate system temperature drift.
Highlights:
- plug-and-play, maintenance-free;
- suitable for industrial applications such as on-site pipelines, open tanks, or sealed storage tanks;
- High measurement accuracy with excellent repeatability;
- Rapid response to changes in the density of heavy liquid.
Contact Lonnmeter now for more applications!
Post time: Jan-18-2025