I. Introduction to Desulfurization Absorber
The main function of the desulfurization absorber is to circulate and spray the slurry mixed with limestone and gypsum through the circulation pump, and the spray layer pipelines to absorb the sulfur dioxide in the flue gas entering the absorber. The sulfur dioxide absorbed by the slurry reacts with the limestone and the oxygen blown into the absorber to produce calcium sulfate dihydrate (gypsum), and then the generated gypsum is discharged to the gypsum dehydration system through the gypsum discharge pump for dehydration.
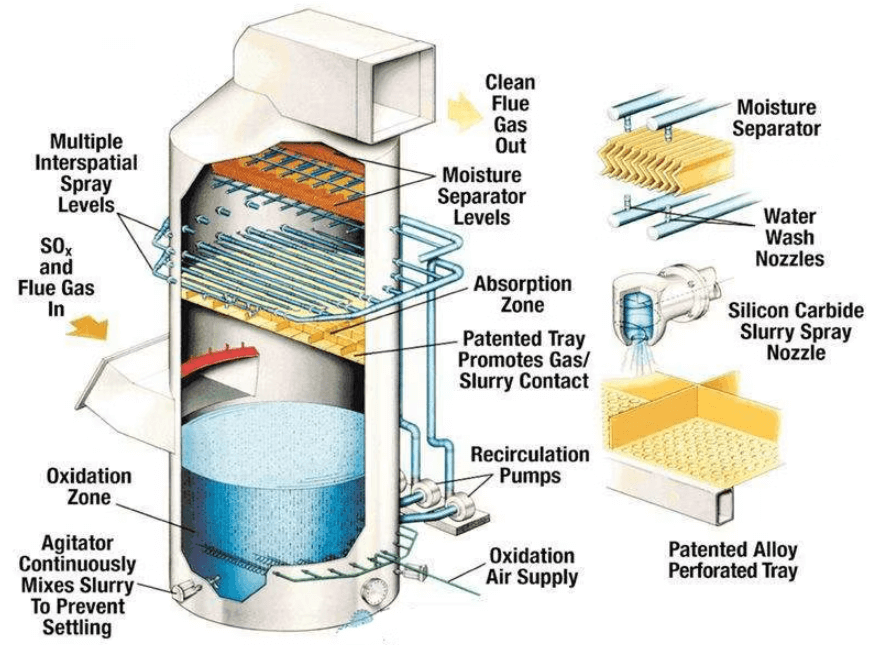
II. Three Functional Areas of the Desulfurization Absorber
The absorber can be divided into three functional areas from top to bottom: oxidation crystallization, absorption and demisting zone.
(1) Oxidation crystallization zone refers to the slurry pool of the absorber, and its main function is to dissolve limestone and oxidize calcium sulfite.
(2) Absorption zone includes the absorber inlet, tray and several layers of sprays. There are many hollow cone nozzles on each layer of spray device; the main function of the absorber rests on acidic pollutant and fly ash absorption in the flue gas.
(3) Demisting zone features two-stage demisters above the spray layer. Its main function is to separate the droplets in the flue gas, reducing the impact on downstream equipment and the dosage of absorbent.
The absorption area of the absorber refers to the area between the center line of the inlet of the absorber and that of the highest spray layer. The sprayed slurry washes the sulfur-containing flue gas in this area. A sufficient height of the absorption area ensures a higher desulfurization rate. The higher the height, the lower the required circulation pump flow rate Under the same requirement on desulfurization rate.
The spray zone of the absorber is defined as:
(1) Spray tower: 1.5m below the lowest nozzle to the outlet area of the highest nozzle.
(2) Liquid column tower: from the outlet of the lowest nozzle to 0.5m above the highest liquid column when all slurry circulation pumps are running.
The absorber is the core device of the flue gas desulfurization system. It requires a large gas-liquid contact area, good gas absorption reaction, small pressure loss. It’s suitable for large-capacity flue gas treatment. The following primary process steps are completed in this device:
① Absorption of harmful gases in washing slurry;
② Separation of flue gas and washing slurry;
③ Neutralization of slurry;
④ Oxidation of intermediate neutralization products into gypsum;
⑤ Gypsum crystallization.
III. Absorber Composition
The absorber is generally divided into a cylinder, a flue gas inlet and a flue gas outlet in structure. The flue gas inlet and outlet are lie out in the middle of the absorber and at the top of the absorber correspondingly in typical. The absorber cylinder can be divided into a slurry pool, a spray layer and a demisting area in function. The slurry pool is located at the lower part of the absorber inlet in general, and the spray layer and the demister are located between the flue gas inlet and outlet. The flue gas outlet of the absorber can be a top direct outlet or a horizontal side outlet.
The conventional spray area features spray layers and nozzles and other devices. Depending on the desulfurization process, the spray area of some absorbers will also be equipped with trays, Venturi rods and other devices.
IV. Design requirements for Absorber
(1) The calcium-sulfur ratio should not be greater than 1.05.
(2) When using an in-tower demister, the flue gas velocity of the absorber under design conditions should not exceed 3.8m/s, which could be monitored by a Coriolis flow meter.
(3) An integrated structure of the slurry pool and the tower body is preferred.
(4) The residence time of slurry circulation should not be less than 4 min, and the liquid column tower should be no less than 2.5 min.
(5) A water retaining ring and a rain cover should be installed at the intersection of the absorber inlet flue and the vertical wall of the absorber.
(6) The inlet flue of the spray empty tower should be arranged in an oblique downward entry manner. When the horizontal entry arrangement is adopted, it should be ensured that the lowest position of the flue at the first elbow adjacent to the absorber inlet is 1.5 to 2m higher than the normal operating liquid level of the absorber slurry pool. The inlet flue of the liquid column tower can be arranged in a horizontal or vertical entry manner.
(7) The distance between adjacent spray layers of the spray empty tower should not be less than 1.8m.
(8) The top spray layer of the empty spray tower should only spray downwards, and the net distance from the lowest layer of the demister should not be less than 2m.
(9) For spray towers equipped with porous trays and tabulators, the porous trays and tabulator blades should be made of alloy anti-corrosion materials.
(10) When the exhaust gas heating and heat exchange device is not installed, the selection of design parameters such as the empty tower flow rate, liquid-gas ratio, and slurry solid content of the absorber should take into account the requirements of desulfurization efficiency and the influence of factors such as reducing the amount of net flue gas droplets carried.
(11) The design of the absorber should be adapted to the design range of boiler load and coal sulfur content. An intelligent non-nuclear slurry density meter from Lonnmeter is recommended to monitor density of limestone and gypsum at the outlet to guarantee sufficient desulfurization rate.
Post time: Feb-05-2025