Flotation in Benefication
Flotation maximizes the value of ores by skillfully separating valuable minerals from gangue minerals in mineral processing through the physical and chemical differences. Whether dealing with nonferrous metals, ferrous metals, or nonmetallic minerals, flotation plays a critical role in providing high-quality raw materials.
1. Flotation Methods
(1) Direct Flotation
Direct flotation refers to filter valuable minerals from a slurry by allowing them to adhere to air bubbles and float to the surface, while gangue minerals remain in the slurry. This method is critical in the beneficiation of nonferrous metals. For example, ore processing comes to the flotation stage after undergoing crushing and grinding in copper ore processing, in which specific anionic collectors are introduced to alter the hydrophobicity and leave them to adsorb on the surface of copper minerals. Then hydrophobic copper particles attach to air bubbles and rise, forming a layer of froth featuring rich copper. This froth is collected in preliminary concentration of copper minerals, which serves as a high-grade raw material for further refinement.
(2) Reverse Flotation
Reverse flotation involves floating the gangue minerals while the valuable minerals remain in the slurry. For instance, in iron ore processing with quartz impurities, anionic or cationic collectors are used to alter the chemical environment of the slurry. This changes the hydrophilic nature of quartz to hydrophobic, allowing it to attach to air bubbles and float.
(3) Preferential Flotation
When ores contain two or more valuable components, preferential flotation separates them sequentially based on factors like mineral activity and economic value. This step-by-step flotation process ensures each valuable mineral is recovered with high purity and recovery rates, maximizing resource utilization.
(4) Bulk Flotation
Bulk flotation treats multiple valuable minerals as a whole, floating them together to obtain a mixed concentrate, followed by subsequent separation. For example, in copper-nickel ore beneficiation, where copper and nickel minerals are closely associated, bulk flotation using reagents like xanthates or thiols allows the simultaneous flotation of sulfide copper and nickel minerals, forming a mixed concentrate. Subsequent complex separation processes, such as using lime and cyanide reagents, isolate high-purity copper and nickel concentrates. This "collect-first, separate-later" approach minimizes the loss of valuable minerals in the initial stages and significantly improves overall recovery rates for complex ores.
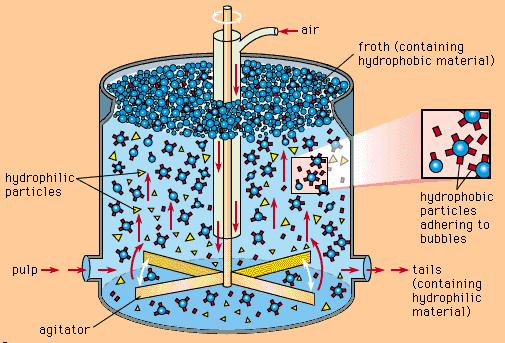
2. Flotation Processes: A Step-by-Step Precision
(1) Stage Flotation Process: Incremental Refinement
In flotation, stage flotation guides the processing of complex ores by dividing the flotation process into multiple stages.
For example, in a two-stage flotation process, the ore undergoes rough grinding, partially liberating valuable minerals. The first flotation stage recovers these liberated minerals as preliminary concentrates. The remaining unliberated particles proceed to a second grinding stage for further size reduction, followed by a second flotation stage. This ensures the remaining valuable minerals are thoroughly separated and combined with the first-stage concentrates. This method prevents overgrinding in the initial stage, reduces resource waste, and improves flotation precision.
For more complex ores, such as those containing multiple rare metals with tightly bound crystal structures, a three-stage flotation process may be used. Alternating grinding and flotation steps allow for meticulous screening and ensure each valuable mineral is extracted with maximum purity and recovery rate, laying a strong foundation for further processing.
3. Key Factors in Flotation
(1) pH Value: The Subtle Balance of Slurry Acidity
The pH value of the slurry plays a pivotal role in flotation, profoundly influencing mineral surface properties and reagent performance. When the pH is above a mineral's isoelectric point, the surface becomes negatively charged; below it, the surface is positively charged. These changes in surface charge dictate the adsorption interactions between minerals and reagents, much like the attraction or repulsion of magnets.
For example, under acidic conditions, sulfide minerals benefit from enhanced collector activity, making it easier to capture target sulfide minerals. Conversely, alkaline conditions facilitate the flotation of oxide minerals by modifying their surface properties to enhance reagent affinity.
Different minerals require specific pH levels for flotation, necessitating precise control. For instance, in the flotation of quartz and calcite mixtures, quartz can be floated preferentially by adjusting the slurry pH to 2-3 and using amine-based collectors. Conversely, calcite flotation is favored in alkaline conditions with fatty acid-based collectors. This precise pH adjustment is key to achieving efficient mineral separation.
(2) Reagent Regime
The reagent regime governs the flotation process, encompassing the selection, dosage, preparation, and addition of reagents. Reagents selectively adsorb onto target mineral surfaces, altering their hydrophobicity.
Frothers stabilize bubbles in the slurry and facilitate the flotation of hydrophobic particles. Common frothers include pine oil and cresol oil, which form stable, well-sized bubbles for particle attachment.
Modifiers activate or inhibit mineral surface properties and adjust the chemical or electrochemical conditions of the slurry.
Reagent dosage requires precision—insufficient amounts reduce hydrophobicity, lowering recovery rates, while excessive amounts waste reagents, increase costs, and compromise concentrate quality. Intelligent devices such as online concentration meter can realize accurate control of reagent dosages.
The timing and method of reagent addition are also critical. Adjusters, depressants, and some collectors are often added during grinding to prepare the slurry's chemical environment early. Collectors and frothers are typically added in the first flotation tank to maximize their effectiveness at critical moments.
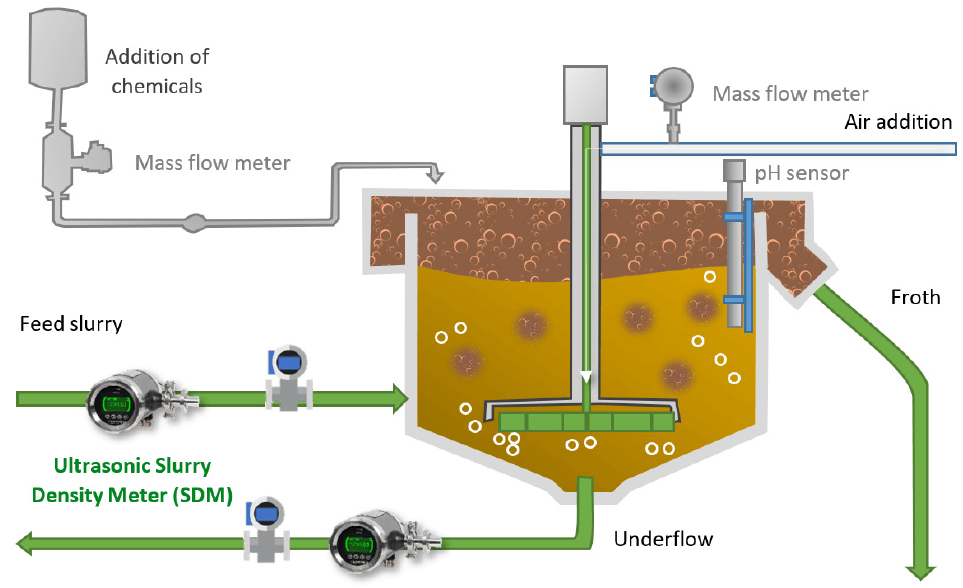
(3) Aeration Rate
Aeration rate creates optimal conditions for mineral-bubble attachment, making it an indispensable factor in flotation. Insufficient aeration results in too few bubbles, reducing collision and attachment opportunities, thereby impairing flotation performance. Over-aeration leads to excessive turbulence, causing bubbles to break and dislodging attached particles, reducing efficiency.
Engineers employ methods like gas collection or anemometer-based airflow measurement to fine-tune aeration rates. For coarse particles, increasing aeration to generate larger bubbles improves flotation efficiency. For fine or easily floated particles, careful adjustments ensure stable and effective flotation.
(4) Flotation Time
Flotation time is a delicate balance between concentrate grade and recovery rate, requiring precise calibration. In the early stages, valuable minerals rapidly attach to bubbles, leading to high recovery rates and concentrate grades.
Over time, as more valuable minerals are floated, gangue minerals may also rise, diluting concentrate purity. For simple ores with coarser-grained and easily floated minerals, shorter flotation times suffice, ensuring high recovery rates without sacrificing concentrate grade. For complex or refractory ores, longer flotation times are necessary to allow fine-grained minerals sufficient interaction time with reagents and bubbles. Dynamic adjustment of flotation time is a hallmark of precise and efficient flotation technology.
Post time: Jan-22-2025