In the limestone-gypsum wet flue gas desulfurization system, maintaining the quality of the slurry is critical for the safe and stable operation of the entire system. It directly impacts equipment lifespan, desulfurization efficiency, and by-product quality. Many power plants underestimate the effect of chloride ions in the slurry on the FGD system. Below are the hazards of excessive chloride ions, their sources, and recommended improvement measures.
I. Hazards of Excessive Chloride Ions
1. Accelerated Corrosion of Metal Components in the Absorber
- Chloride ions corrode stainless steel, breaking down the passivation layer.
- High concentrations of Cl⁻ lower the pH of the slurry, leading to general metal corrosion, crevice corrosion, and stress corrosion. This damages equipment such as slurry pumps and agitators, significantly shortening their lifespan.
- During absorber design, the allowable Cl⁻ concentration is a key consideration. Higher chloride tolerance requires better materials, increasing costs. Typically, materials like 2205 stainless steel can handle Cl⁻ concentrations up to 20,000 mg/L. For higher concentrations, more robust materials like Hastelloy or nickel-based alloys are recommended.
2. Reduced Slurry Utilization and Increased Reagent/Energy Consumption
- Chlorides mostly exist as calcium chloride in the slurry. High calcium ion concentration, due to the common ion effect, suppresses limestone dissolution, lowering alkalinity and affecting the SO₂ removal reaction.
- Chloride ions also hinder the physical and chemical absorption of SO₂, reducing desulfurization efficiency.
- Excess Cl⁻ can cause bubble formation in the absorber, leading to overflow, false liquid level readings, and pump cavitation. This can even result in slurry entering the flue gas duct.
- High chloride concentrations can also cause strong complexation reactions with metals like Al, Fe, and Zn, reducing the reactivity of CaCO₃ and ultimately decreasing slurry utilization efficiency.
3. Deterioration of Gypsum Quality
- Elevated Cl⁻ concentrations in the slurry inhibit SO₂ dissolution, leading to higher CaCO₃ content in the gypsum and poor dewatering properties.
- To produce high-quality gypsum, additional washing water is required, creating a vicious cycle and increasing the chloride concentration in wastewater, complicating its treatment.
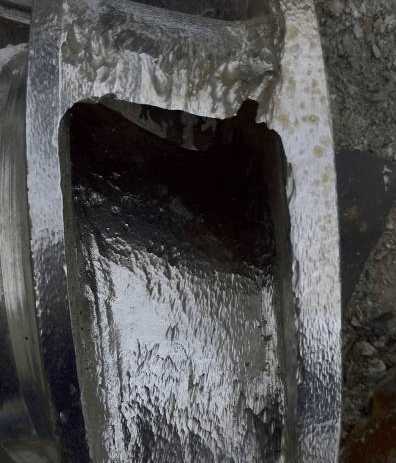
II. Sources of Chloride Ions in Absorber Slurry
1. FGD Reagents, Makeup Water, and Coal
- Chlorides enter the system through these inputs.
2. Using Cooling Tower Blowdown as Process Water
- Blowdown water typically contains around 550 mg/L of Cl⁻, contributing to slurry Cl⁻ accumulation.
3. Poor Electrostatic Precipitator Performance
- Increased dust particles entering the absorber carry chlorides, which dissolve in the slurry and accumulate.
4. Inadequate Wastewater Discharge
- Failure to discharge desulfurization wastewater per design and operational requirements leads to Cl⁻ accumulation.
III. Measures to Control Chloride Ions in Absorber Slurry
The most effective method to control excessive Cl⁻ is to increase the discharge of desulfurization wastewater while ensuring compliance with discharge standards. Other recommended measures include:
1. Optimize Filtrate Water Use
- Shorten the filtrate recirculation time and control the inflow of cooling water or rainwater into the slurry system to maintain water balance.
2. Reduce Gypsum Washing Water
- Limit gypsum Cl⁻ content to a reasonable range. Increase the removal of Cl⁻ during dewatering by replacing slurry with fresh gypsum slurry when Cl⁻ levels exceed 10,000 mg/L. Monitor slurry Cl⁻ levels with an inline density meter and adjust wastewater discharge rates accordingly.
3. Strengthen Chloride Monitoring
- Regularly test slurry chloride content and adjust operations based on coal sulfur levels, material compatibility, and system requirements.
4. Control Slurry Density and pH
- Maintain the slurry density between 1080–1150 kg/m³ and pH between 5.4–5.8. Periodically lower the pH to improve reactions within the absorber.
5. Ensure Proper Operation of Electrostatic Precipitators
- Prevent dust particles carrying high chloride concentrations from entering the absorber, which would otherwise dissolve and accumulate in the slurry.
Conclusion
Excess chloride ions indicate inadequate wastewater discharge, leading to reduced desulfurization efficiency and system imbalances. Effective chloride control can significantly enhance system stability and efficiency. For tailored solutions or to try Lonnmeter's products with professional remote debugging support, contact us for a free consultation on slurry density measurement solutions.
Post time: Jan-21-2025