Flue gas desulfurization in refinery weighs in reducing the risks of acid rains and enhancing air quality. For the purpose of improving efficiency and cost saving, the amount of desulfurizer is ought to adjust up to rigorous standards. Traditional desulfurization relies on manual adjustments or fixed ratios, which means inescapable errors and series of waste.
The application of inline density meters is a guarantee of precise control of desulfurizer in real-time, reducing operational costs, chemical consumption and even further environmental consumption.
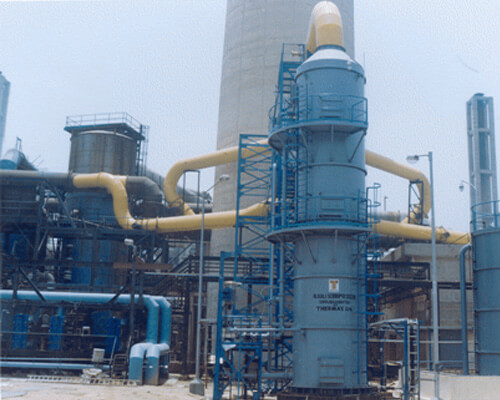
Challenges in Refinery Flue Gas Desulfurization
The primary challenge in refinery flue gas desulfurization lies in precise control over the dosage of desulfurizers. The desulfurizers like lime, sodium hydroxide or others reacts with sulfur compounds on the flue gas and then generates related byproducts. The dosage of desulfurizer depends on specific concentration of sulfur compounds in emissions.
Nevertheless, the flue gas in dynamic changes makes it difficulty in technology to determine the concentration of desulfurizers precisely. The amount of desulfurizer will be excessive or insufficient, and those two statuses lead to corresponding outcomes in the process of desulfurization. Let's dive into those two conditions in detail.
Excessive desulfurizer entering into sulfur compounds results in cost increasing, especially in large-scale processing. In addition, excessive desulfurization gives rise to higher concentration of acidic liquids and superfluous waste water, which causes additional costs of waste water treatment. Last but not the least, excessive desulfurizers increase risks of corrosion in pipes and devices, then the over acidic liquids may lead to higher frequency of maintenance and replacement.
On the contrary, insufficient desulfurizers lower the efficiency of the desulfurization process, so sulfur compounds remain in the flue gas at a certain concentration. It turns out to be failed to meet emission standards, generating negative effects on both safety production and compliance with environmental regulations.
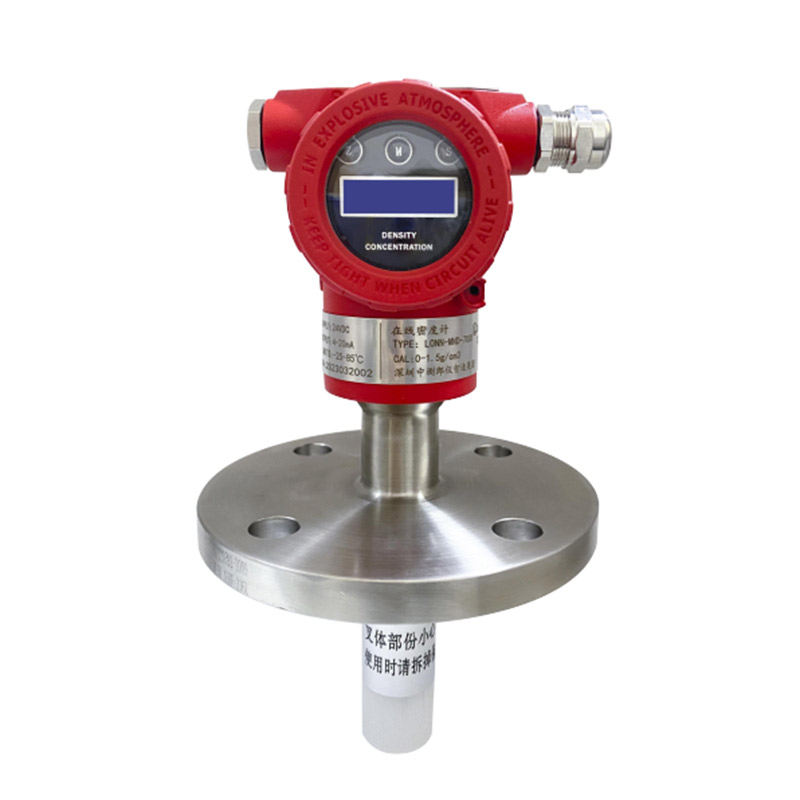
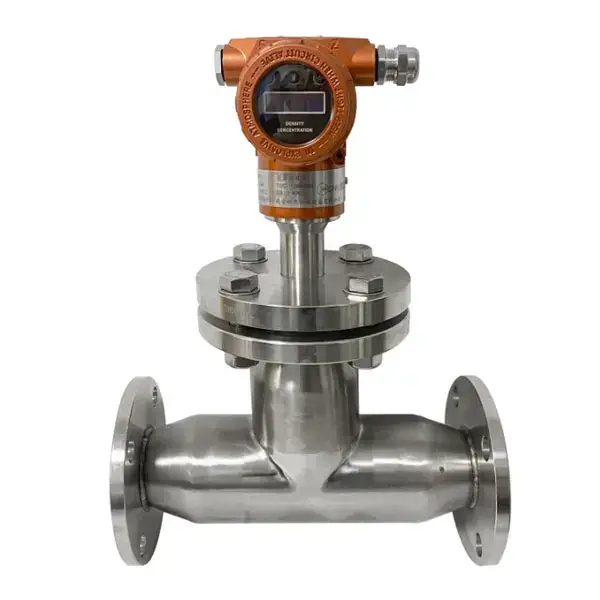
Advantages of Inline Density Meters
In order to increase efficiency of repeated work and reduce unnecessary manual errors, inline density meters are one of the best options in practical industrial processing. Following obvious advantages are all reasons to select the accurate online density meters.
Accurate Controlling Over Amount of Desulfurizers
The desulfurizer reacts with sulfur compounds in the desulfurization process in compliance with rigorous regulations. The density of desulfurization liquid changes as the decreasing of sulfur compounds concentration in typical.
The density fluctuations are monitored continuously and conveyed to the data collection system in electrical signals, which makes real-time adjustment possible by controlling the removal rate of sulfur compounds. The intelligent online density meter is able to increase or decrease the added desulfurizers according to density automatically, preventing overuse or insufficient dosing.
Improved Reaction Efficiency and Reduced Waste
By precisely controlling the dosage of the desulfurizing agent, the density meter ensures that the desulfurization process is as efficient as possible, while minimizing unnecessary chemical waste. This, in turn, lowers operational costs.
Lowering Influences on Environment
The intelligent density meter reduces operational cost and the amount of harmful chemicals released into the air. By easing the load of wastewater treatment, the chemical pollution in wastewater is reduced greatly. At the same time, the risks of air pollution are lowered, too.
Outstanding adaptability to Changing Operating Conditions
The composition of refinery flue gas is complex, and temperature and pressure conditions fluctuate significantly. Insertion-type online density meters are typically designed to withstand high temperatures, high pressures, and corrosive environments, ensuring stable operation and accurate data collection under these challenging conditions.
Applications
Flue gas desulfurization (FGD) is widely used in coal-fired or oil-burned power plants. The online density meter could be used in the following pipelines:
Limestone slurry production line
Limestone slurry feed into Absorber
Gypsum recirculation line in the Absorber
Calcium sulfite slurry line reaching the oxidizer
Gypsum self-drain loop
Installation
The online density meter could be installed via simple insertion rather than system shut down and reconstruction of pipelines. Besides, it's available for a wide range of wetted material applications. Each meter could be installed at a vertical pipe with the slurry flowing upwards. Installation at such the angle could protect the vibrating tines from abrasive slurry while measure the flowing fresh material to keep its precision.
All in all, customers benefit from online density meters in the following aspects:
1. Simple and low-cost installation - It reduces the cost of instrumentation to about $500-$700 per meter
2. Enhanced control of Calcium Carbonate - those meters costs to optimize process and raw material.
3. Extended lifetime of Density Meter - The maintenance and operation cost reduced greatly for the sake of resistance to abrasive fluids.
The application of insertion-type online density meters in refinery flue gas desulfurization processes has proven to be an effective solution for addressing challenges such as excessive desulfurizing agent usage, rising operational costs, and environmental pollution. By monitoring the density changes in real time, the density meters enable precise control of the desulfurizing agent dosage, improving the efficiency of the desulfurization process, reducing waste, and minimizing environmental impact. This technology not only optimizes the use of chemical agents but also contributes to cost reduction and environmental sustainability, making it a valuable tool for modern refining operations.
Post time: Dec-25-2024