Inline density meters are the game changer of denitration in power plants during industrial processes. These innovative intelligent gauges allow operators to monitor density in real-time, also significant devices addressing complex chemical processes. It's essential for operators to face up with operational challenges as observing more and more rigorous environmental regulations. Look into detailed circumstances in which they work to solve complex industrial problems and eliminate cumbersome but repetitive work.
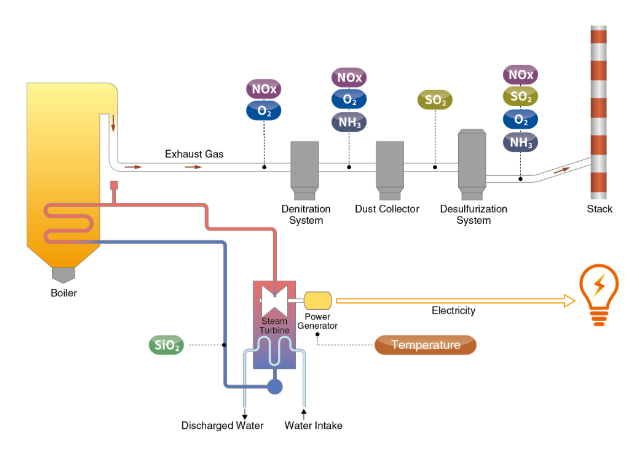
Tricky Technical Dilemmas in Denitration
Adjustments in emissions of nitrogen oxide (NOx) is not a simple task. Nitrogen oxide could not be eliminated completely, no matter in coal-fired, oil-burned or even biomass fueling plants. Emissions management with precision is related to Selective Catalytic Reduction (SCR) or Selective Non-Catalytic Reduction (SNCR), in which reagents are added into flue gas stream for further reaction. Nevertheless, precision dosing monitoring in real time faces multi-challenges from complex operational conditions. Inaccuracy in measurement may cause ammonia slip and reagents waste.
Lonnmeter design and produce the inline density meter for continuous concentration measurement to avoid human errors in traditional sampling. Human sampling relies more on periodic checks and indirect estimations. Such an online density meter is able to detect slight fluctuations in density monitoring to assist precise adjustments, keeping the whole denitration processes stable and efficient.
In addition, it also works in offering parameters indicating mixing quality, reagent consistency and even flow rate. For instances, inconsistency of urea stream to dissolving into water disrupts the reaction chemistry. By monitoring the slurry directly in the pipeline, inline density meters ensure that the desired concentration is maintained from storage to injection, reducing the risk of process inefficiencies or environmental noncompliance.
Recommended Industrial Density Meters
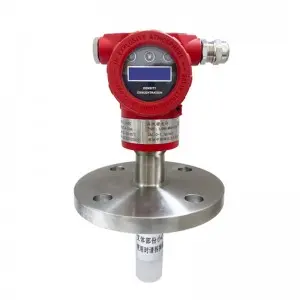
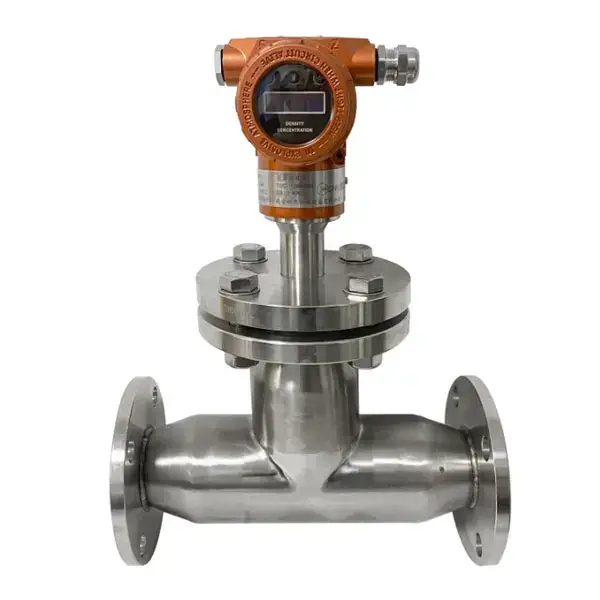
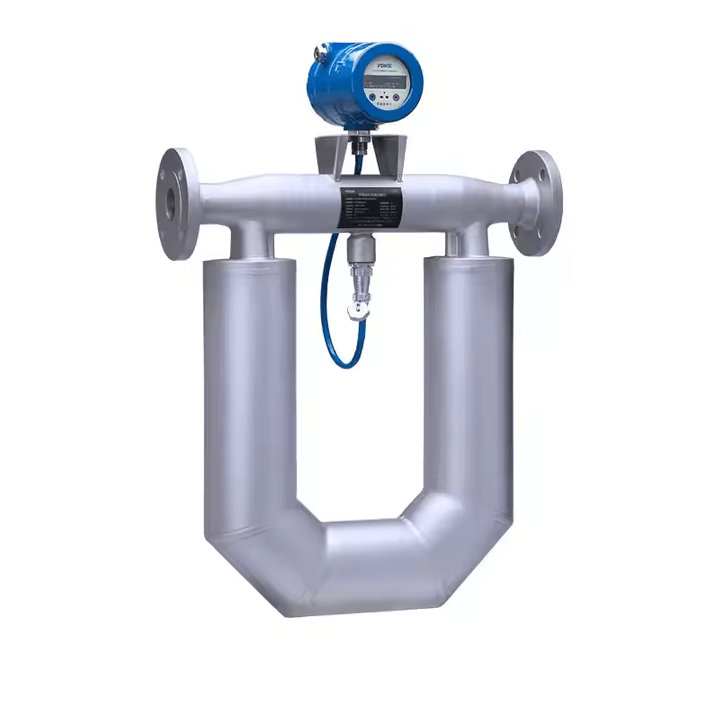

Improving Automation in Denitration and System Reliability
Gone are the days when plant operators had to rely on manual interventions to fine-tune reagent injection. Modern inline density meters integrate seamlessly into advanced Distributed Control Systems (DCS) or Programmable Logic Controllers (PLC), allowing for a fully automated feedback loop. When density readings deviate from the preset range, the system automatically adjusts the reagent flow rate or dilutes the solution as needed. This automation not only reduces the burden on operators but also eliminates the delays associated with human decision-making.
It's important to balance chemical streams in combined desulfurization and denitration processing, where lime slurry and ammonia solutions are used at the same time. Monitoring density of those two fluids is the prerequisite for normal operation of desulfurization and denitration. This level of coordination helps prevent common issues like sedimentation in limestone pipelines or overdosing of ammonia, both of which can result in costly shutdowns or maintenance.
Besides, such durable inline density meters are resistant to harsh conditions in power plant. For special designs to withstand high temperatures and pressures, they are ideal to handle corrosive chemicals in challenging circumstances like flue gas denitration system.
Applications of Inline Density Meters in Coal-Fired Power Plant
In general, coal-fired power plants are bothering with inefficiencies in density measurement and related technical problems in series, including but not limited to pipeline clogging, ammonia slip and potential maintenance. The fork inline density meter is the ideal intelligent instrument to both the ammonia injection line and the limestone slurry system.
The results were transformative. Real-time density monitoring allowed the plant to fine-tune reagent dosing with unprecedented accuracy. Ammonia slip levels dropped by over 90%, while NOx reduction efficiency exceeded 92%. The limestone slurry, which had previously caused scaling and blockages, was maintained at the optimal density, eliminating unscheduled maintenance and reducing downtime by 20%. These improvements not only brought the plant into compliance with environmental standards but also reduced operational costs by 15%.
Why Inline Density Meters Are Indispensable
What sets inline density meters apart from other monitoring solutions is their versatility and adaptability. They are not limited to denitration; their applications extend to any industrial process requiring precise fluid management. In the context of power plants, this includes desulfurization systems, wastewater treatment, and fuel blending operations. Their ability to provide real-time, accurate, and actionable data makes them a cornerstone of modern process optimization.
By implementing these instruments, power plants can achieve a level of process control that was previously unattainable. The benefits extend beyond compliance and efficiency; they also include improved equipment longevity, reduced maintenance costs, and enhanced sustainability. For operators who value both performance and environmental responsibility, inline density meters are not just an investment—they are a necessity.
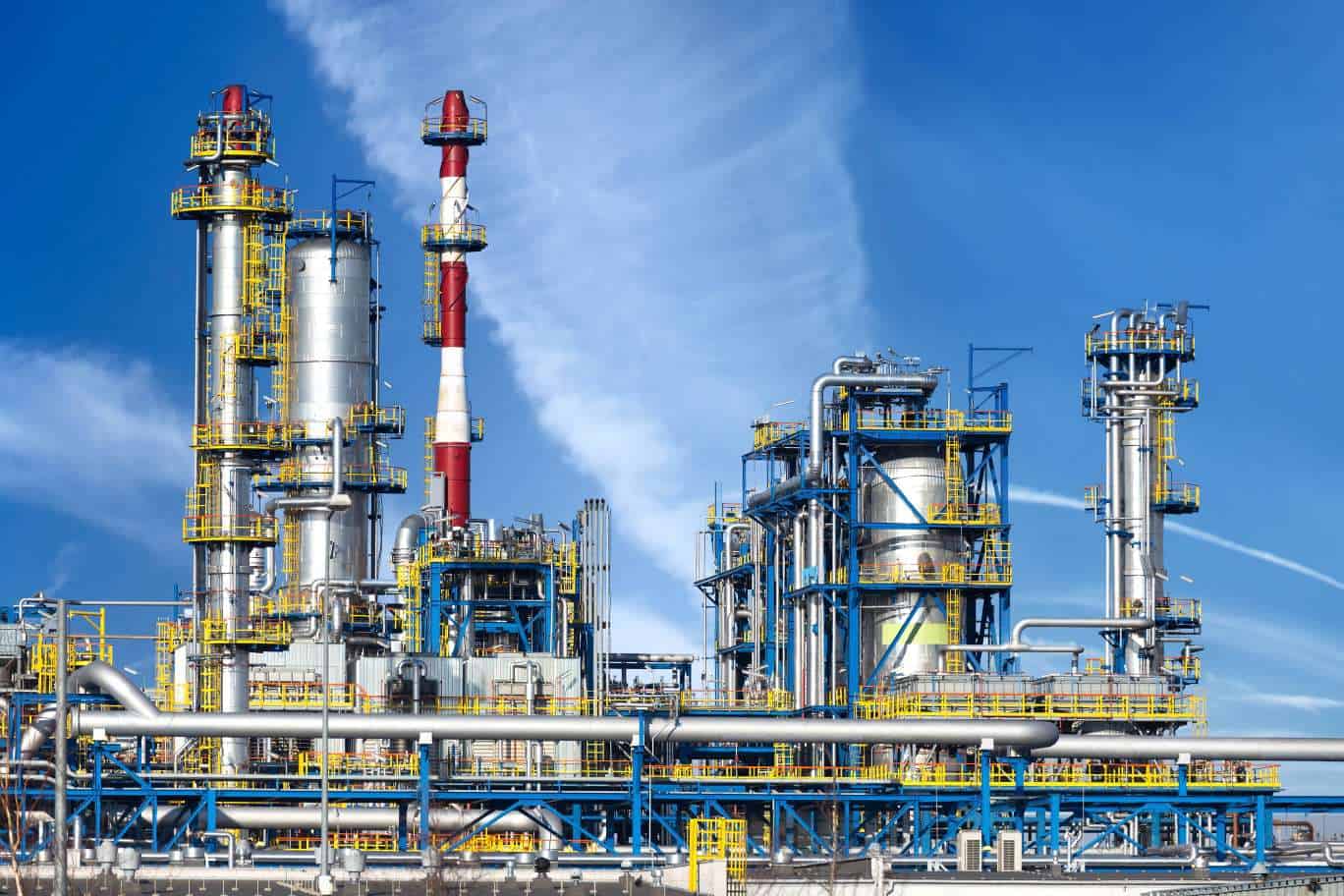
Conclusion
The adoption of inline density meters in denitration systems exemplifies how advanced technology can transform industrial processes. By addressing challenges like reagent consistency, ammonia slip, and process automation, these instruments enable power plants to operate more efficiently, sustainably, and profitably. Their proven track record in real-world applications underscores their value as a critical tool in the fight against NOx emissions. If you’re looking to elevate your denitration operations, there’s no better time to explore the potential of inline density measurement.
Post time: Dec-27-2024