Pulp Concentration Measurement
The pulp concentration in the machine chest reaches 2.5–3.5% in general. Water is required to dilute the pulp to a lower concentration for well-dispersed fibers and impurity removal.
For fourdrinier machines, the pulp concentration entering the mesh is 0.3–1.0% in typical according to the pulp characteristics, equipment properties, and paper quality. At this stage, the level of dilution corresponds to the required pulp concentration on mesh, meaning the same concentration is used for purification, filtration, and forming on the mesh.
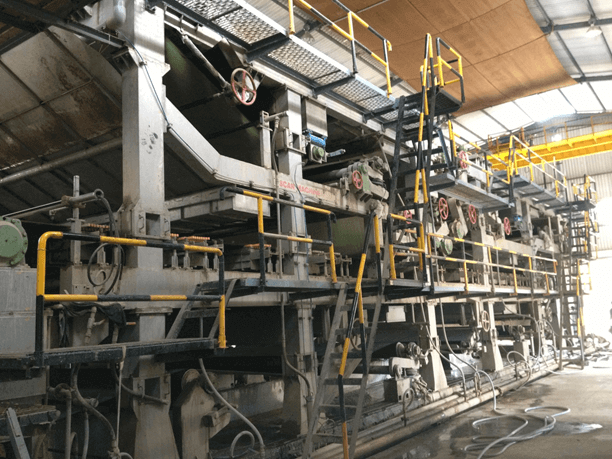
The pulp concentration on mesh is lower to 0.1–0.3% only for cylinder machines. Flow rate through the purification and filtration is higher than requirements with such low-concentration pulp. Furthermore, more purification and filtration devices are needed to process the low-concentration pulp, requiring more capital, larger space, more complex pipelines, and higher energy consumption.
Cylinder machines often adopt a two-stage dilution process, in which the concentration is lowered to 0.5~0.6% firstly for preliminary purification and filtration; then lowered to target concentration further before entering onto mesh in stabilizing box.
Pulp dilution uses white water through the mesh in typical for water conservation and recovery of fine fibers, fillers, and chemicals from the white water. White water recovery is benefit to energy conservation for machines requiring pulp heating.
Key Factors Affecting Diluted Pulp Concentration
Variations in Pulp Concentration Entering the Regulating Box
Fluctuations in the consistency from the beating or changes in the broke system can cause variations in pulp concentration. Poor circulation in machine chests can lead to inconsistent pulp concentration across different areas, causing further instability.
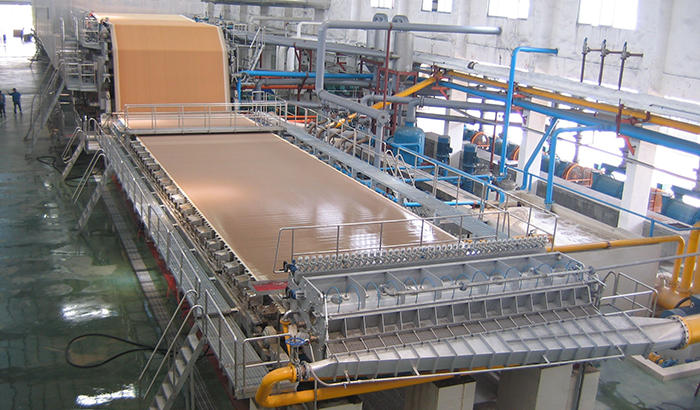
Backflow of Rejects in Purification and filtration
The reject from purification and filtration is typically reintroduced into the system with the dilution water. Variations in the volume and concentration of this reject depend on the performance of the purification and filtration equipment and the liquid levels at the pump inlets.
These changes generate impacts on the white water concentration used for dilution and, in turn, the final pulp concentration. Similar issues can occur in the return systems of cylinder machine overflow tanks.
Variations in diluted pulp concentration can affect both the operation of paper machine and the final paper quality. Therefore, it is essential to closely monitor pulp concentration with consistency meter pulp manufactured by Lonnmeter during production and adjust the inflow to the regulating box to maintain stable concentrations. Modern paper machines often employ automated instruments to:
- Automatically adjust the pulp concentration entering the regulating box.
- Adjust the inflow based on changes in paper basis weight and headbox pulp concentration.
This ensures a stable pulp concentration.
Benefits of Concentration Adjustment for Diluted Pulp
Concentration regulation of diluted pulp benefits to both optimal operation of paper machine and paper quality maintaining.
For Cylinder Machines
When pulp has a low beating degree and dewaters quickly, the internal and external water levels in the mesh section are reduced, weakening the attachment of the paper layer to the mesh. This increases the concentration effect, reduces overflow, and increases the speed differential between the pulp and mesh, leading to uneven paper formation.
To address this, white water usage is increased to lower the pulp concentration, increasing the flow rate to the mesh. This raises the water level differential, increases overflow, reduces concentration effects, and minimizes speed differentials, thereby improving sheet uniformity.
For Fourdrinier Machines
High beating degrees make drainage difficult, extend the waterline, increase moisture in the wet sheet, and lead to embossing or crushing during pressing. Paper tension across the machine reduces, and shrinkage during drying increases, causing defects like folds and wrinkles.
To overcome these challenges, diluted pulp concentration can be increased by reducing white water usage, alleviating drainage issues.
Conversely, if the beating degree is low, fibers tend to flocculate, and drainage occurs too quickly on the mesh, affecting paper uniformity. In this case, increasing white water usage to lower the diluted pulp concentration can reduce flocculation and improve uniformity.
Conclusion
Dilution is a critical operation in papermaking. In production, it is essential to:
- Closely monitor and strictly control changes in diluted pulp concentration to ensure stable operations.
- Pay attention to changes in product quality and operating conditions and, when necessary, adjust pulp concentration as a tool to overcome difficulties like those mentioned above.
By effectively managing pulp dilution, stable production, high-quality paper, and optimal operation can be achieved.
Post time: Jan-24-2025