Pulping matters before paper making, leaving great impacts on the normal operation of the paper machine and the quality of the paper. The key factors in the beating are pulp concentration, beating degree, and pulp ratio.
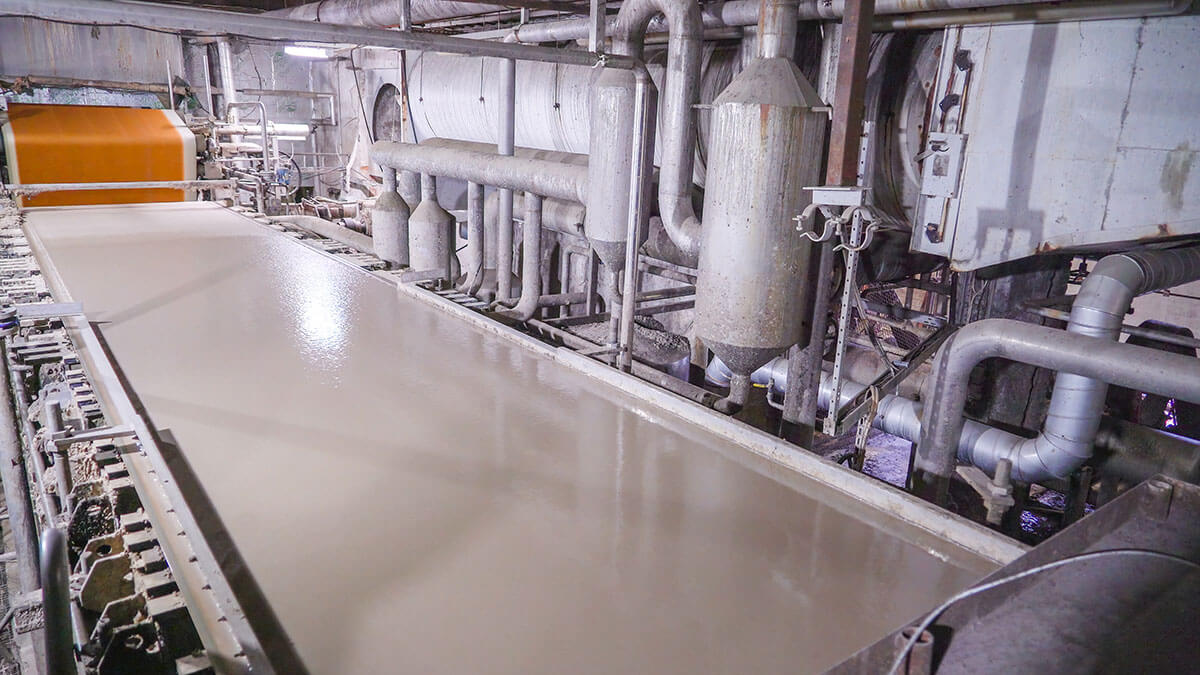
Pulp Concentration Measurement
Unstable pulp concentration can lead to inconsistent paper quality, and it can cause paper breaks and disrupt normal paper making even worse. Factors of unstable pulp concentration instability rest on changing concentration of raw pulp and waste stuff, manual concentration tuning in beating, concentrating and blending, as well as unbalanced whitewater system.
Changes in Raw Pulp Concentration
The pulp delivered from the pulping workshop varies in concentration. The final pulp concentration will be affected in case necessary adjustments haven’t been made in concentrating.
Concentration Adjustment in the Beating
During beating, pulp undergoes processes like concentrating, beating, and mixing, requiring concentration adjustments. Some systems use pulp density meter, but manual adjustments are more common. Concentration changes may occur due to operator inexperience, lack of diligence, or equipment malfunction.
Variations in Waste Stuff Concentration
Recycled broken paper is chopped in a hydropulper and then concentrated to a stable level before dilution to the required process concentration. If the waste stuff concentration varies significantly during dehydration and dilution, it can destabilize the overall pulp system.
Instability in White Water Systems
White water is reused for pulp dilution to reduce water usage and fiber loss. If the white water system is unbalanced or its pressure and flow are unstable, it will impact pulp dilution and concentration.

Beating Degree
Several factors influence pulp beating, such as pressure, concentration, flow rate, time, temperature, blade condition, and operator skill. If any step is mishandled, the pulp beating quality will be impacted. Stabilizing beating is challenging without continuous monitoring, but is essential for stable papermaking.
1. Effects of Low Beating Degree
When the beating is too low, the primary and secondary walls of the fibers are not adequately broken down. Fiber swelling, cutting, fibrillation, and fines formation do not meet process requirements.
This results in excessively fast drainage during forming, poor fiber bonding, and uneven sheet structure, impacting uniformity, strength, and smoothness.
2. Effects of High Beating Degree
Increased beating improves bonding strength but reduces average fiber length and wet web weight.
Over-beating accelerates fiber cutting, swelling, and fibrillation, making drainage on the wire more difficult, extending the waterline, and increasing moisture content in the wet web.
Excess moisture can cause embossing or multiple breaks due to insufficient press pressure.
High beating also increases drying shrinkage, leading to changes in speed ratios across machine sections, affecting sheet dimensions, and reducing strength and stability.
Pulp Ratio
The pulp ratio depends on factors like raw material characteristics, pulping method, machine performance, and paper type and quality requirements. After determining the ratio conditions, strict adherence to the process is crucial to avoid production disruptions and increased costs.
Long vs. Short Fiber Ratio
An appropriate ratio enhances fiber bonding, sheet uniformity, and strength while reducing costs and improving efficiency.
Too little long fiber reduces bonding strength and wet sheet strength, causing breaks, while excessive long fiber is economically unfeasible.
Special Considerations
Chemical grass pulp, with short fibers, thick cell walls, and high hemicellulose content, complicates papermaking and impacts quality. To mitigate these issues, higher-quality long fiber materials, such as cotton, wood, or flax pulp, may be mixed in, despite their higher cost. Proper blending of long and short fibers is key to ensuring smooth papermaking, meeting quality standards, and achieving cost efficiency.
Post time: Jan-24-2025