Are you bothering with too much water in the underflow and solids in the overflow? Do you intend to optimize the thickener operation through eliminating repeated density measurement and human errors? Many end-users face the same problems in the mineral processing industry to save water and collect valuable material for processing. Real-time density meter works efficient in reaching these goals.
The following article concentrates on describing the purposes and benefits of density control at different points of thickener tanks. Let's begin with a concise introduction to the thickening process, followed by five reasons for density measuring in the separation process.
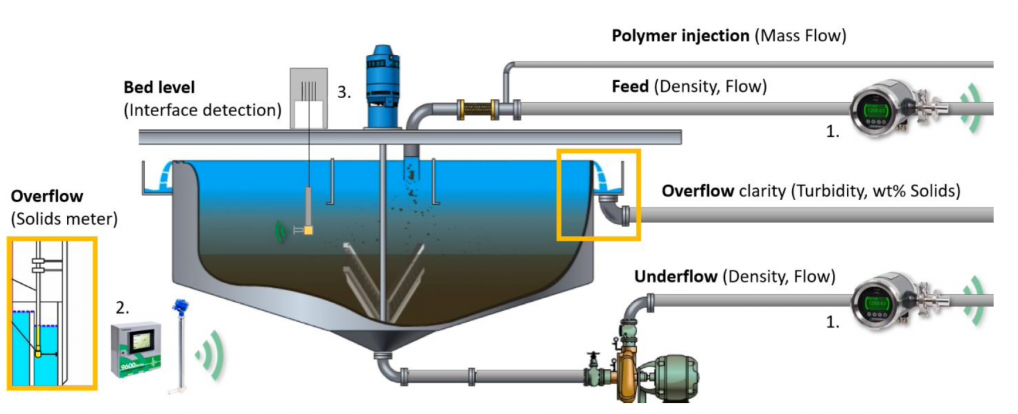
What is the Function of Thickening?
The thickening process involves the separation of a solid-liquid mixture to a dense underflow and a clear overflow in typical. The former consists of solid particles and the latter excludes impurities as much as possible. The separation process is the outcome of gravity. All particles in different sizes and densities form different layers through the tank.
Thickening processes happen in the sedimentation tank in the mineral processing for separation of concentrates and tailings.
Necessary Measuring Points in Thickening
Online liquid density meters are needed to optimize operation of thickeners. For example, installation points include the feed, underflow, overflow and interior of the thickener tank. In above conditions, these sensors could be taken as the slurry density meter or sludge density meter. They are also helpful in improving automatic control of drives, pumps and for efficient dosing of flocculants.
Reasons for Density Measuring
Reasons for density measurement may vary one by one. The following five conditions highlight the importance of density monitoring for industrial optimization.
No. 1 Water Recovery
Water is regarded as one of the most significant assets in mining and mineral industry. Therefore, water recovery or water reuse saves cost of thickening greatly. A small growth of 1-2% in underflow density means large amounts of water needed to operating installations. The increasing of density works effective in guaranteeing firmness in tailing dams, which may collapse in case there is too much liquid pumped to the dams.
No. 2 Mineral Recovery
In concentrate thickeners, the feed typically originates from the flotation circuit. Flotation involves separating particles via gravity. In other words, those with attached air bubbles rise to the surface and are removed, while others remain in the liquid phase. When this process occurs in the product thickener, foam can carry solids into the overflow.
These solids are valuable and, if not recovered, can reduce the overall recovery rate of concentrated metal. Additionally, solids in the overflow can lead to higher reagent costs, damage to pumps and valves, and increased maintenance expenses, such as cleaning process water tanks when solids accumulate there.
About 90% of the solids lost in the overflow are eventually recovered in later stages of the process (e.g., in tanks and dams). However, the remaining 10%, which represents a significant economic value, is permanently lost. Reducing the loss of solids into the overflow should therefore be a priority. Investing in process control technologies can enhance recovery rates and deliver quick returns on investment.
The use of Lonnmeter density meters and flow meters in the underflow enables better monitoring of thickener performance. Real-time detection of solids in the overflow is also possible with density or solids meters. The instruments’ 4-20mA signals can be integrated into the control system for direct process optimization.
3 Efficient Flocculant Use
Flocculants works in improving sedimentation efficiency, namely chemicals facilitating particles in liquids to clump together. The dosing of flocculants regard the cost control over reagent and operational efficiency. The density meter allows precise and reliable density control for the thickener feed. The goal is to achieve the highest possible solids percentage by weight in the feed slurry while still allowing free particle settling. If the feed slurry density exceeds the target, additional process liquor must be added, and more mixing energy may be required to ensure adequate feed well mixing.
Real-time density measurement of the feed slurry using an inline density meter is crucial for process control. This ensures efficient flocculant use and optimizes the mixing process, keeping the thickener operating within its target range.
4 Immediate Detection of Flocculation Problems
Operators strive to maintain steady conditions in thickeners, achieving a clarified overflow with minimal solids and a dense underflow with minimal liquid. However, process conditions can change over time, potentially leading to poor settling, reduced underflow density, and higher solids in the overflow. These issues can stem from flocculation problems, air or foam in the tank, or an excessively high solids concentration in the feed.
Instrumentation and automation can help operators maintain control by detecting such issues in real time. Beyond inline measurements, tank-based instrumentation like ultrasonic bed level probes can provide critical insights. These “diver” probes move up and down within the tank, profiling mud levels, settling zones, and overflow clarity. Bed level measurements are particularly useful for flocculation control strategies, ensuring consistent performance.
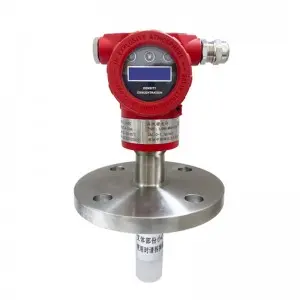
Slurry Density Meter (SDM)
The Slurry Density Meter (SDM) is an eco-friendly alternative to traditional nuclear density meters. It has rapidly gained popularity, with hundreds of installations worldwide. The SDM provides accurate and reliable density measurements, making it an ideal solution for modern mineral processing plants.
Measuring density plays a crucial role in improving thickener efficiency and serves as a key performance indicator for process control. By adopting advanced measurement technologies and process control strategies, operators can optimize thickener performance, enhance recovery rates, and reduce operational costs.
Post time: Dec-30-2024