Analysis of reasons for gypsum dehydration difficulties
1 Boiler oil feeding and stable combustion
Coal-fired power generation boilers need to consume a large amount of fuel oil to assist combustion during startup, shutdown, low-load stable combustion and deep peak regulation due to design and coal burning. Due to unstable operation and insufficient boiler combustion, a considerable amount of unburned oil or mixture of oil powder will enter the absorber slurry with the flue gas. Under the strong disturbance in the absorber, it is very easy to form fine foam and gather on the surface of the slurry. This is the composition analysis of the foam on the surface of the absorber slurry of the power plant.
While the oil is gathering on the surface of the slurry, a part of it is quickly dispersed in the absorber slurry under the interaction of stirring and spraying, and a thin oil film is formed on the surface of limestone, calcium sulfite and other particles in the slurry, which wraps the limestone and other particles, hindering the dissolution of limestone and the oxidation of calcium sulfite, thereby affecting the desulfurization efficiency and the formation of gypsum. The oil-containing absorption tower slurry enters the gypsum dehydration system through the gypsum discharge pump. Due to the presence of oil and incompletely oxidized sulfurous acid products, it is easy to cause the vacuum belt conveyor filter cloth gap to be blocked, which leads to difficulties in gypsum dehydration.
2. Smoke Concentration at Inlet
The wet desulfurization absorption tower has a certain synergistic dust removal effect, and its dust removal efficiency can reach about 70%. The power plant is designed to have a dust concentration of 20mg/m3 at the dust collector outlet (desulfurization inlet). In order to save energy and reduce plant electricity consumption, the actual dust concentration at the dust collector outlet is controlled at about 30mg/m3. Excessive dust enters the absorption tower and is removed by the synergistic dust removal effect of the desulfurization system. Most of the dust particles entering the absorption tower after electrostatic dust purification are less than 10μm, or even less than 2.5μm, which is much smaller than the particle size of gypsum slurry. After the dust enters the vacuum belt conveyor with the gypsum slurry, it also blocks the filter cloth, resulting in poor air permeability of the filter cloth and difficulty in gypsum dehydration.
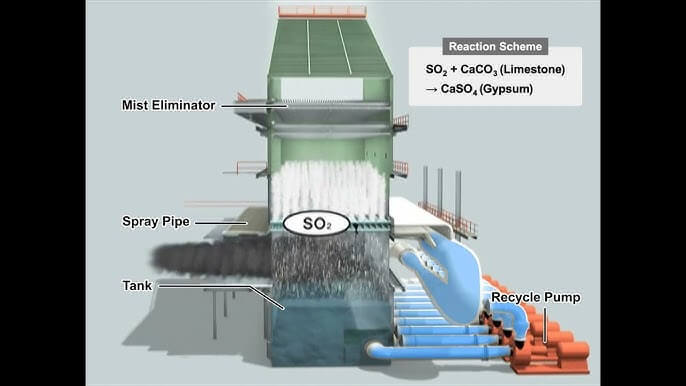
2. Influence of gypsum slurry quality
1 Slurry density
The size of the slurry density indicates the density of the slurry in the absorption tower. If the density is too small, it means that the CaSO4 content in the slurry is low and the CaCO3 content is high, which directly causes the waste of CaCO3. At the same time, due to the small CaCO3 particles, it is easy to cause gypsum dehydration difficulties; if the slurry density is too large, it means that the CaSO4 content in the slurry is high. Higher CaSO4 will hinder the dissolution of CaCO3 and inhibit the absorption of SO2. CaCO3 enters the vacuum dehydration system with the gypsum slurry and also affects the dehydration effect of gypsum. In order to give full play to the advantages of the double-tower double-circulation system of wet flue gas desulfurization, the pH value of the first-stage tower should be controlled within the range of 5.0±0.2, and the slurry density should be controlled within the range of 1100±20kg/m3. In actual operation, the slurry density of the first-stage tower of the plant is about 1200kg/m3, and even reaches 1300kg/m3 at high times, which is always controlled at a high level.
2. Degree of forced oxidation of slurry
Forced oxidation of slurry is to introduce sufficient air into the slurry to make the oxidation of calcium sulfite to calcium sulfate reaction tend to be complete, and the oxidation rate is higher than 95%, ensuring that there are enough gypsum varieties in the slurry for crystal growth. If the oxidation is not sufficient, mixed crystals of calcium sulfite and calcium sulfate will be generated, causing scaling. The degree of forced oxidation of slurry depends on factors such as the amount of oxidation air, the residence time of slurry, and the stirring effect of slurry. Insufficient oxidation air, too short residence time of slurry, uneven distribution of slurry, and poor stirring effect will all cause the CaSO3·1/2H2O content in the tower to be too high. It can be seen that due to insufficient local oxidation, the CaSO3·1/2H2O content in the slurry is significantly higher, resulting in difficulty in gypsum dehydration and a higher water content.
3. Impurity content in slurry Impurities in slurry mainly come from flue gas and limestone. These impurities form impurity ions in slurry, affecting the lattice structure of gypsum. Heavy metals continuously dissolved in smoke will inhibit the reaction of Ca2+ and HSO3-. When the content of F- and Al3+ in slurry is high, fluorine-aluminum complex AlFn will be generated, covering the surface of limestone particles, causing slurry poisoning, reducing desulfurization efficiency, and fine limestone particles are mixed in incompletely reacted gypsum crystals, making it difficult to dehydrate gypsum. Cl- in slurry mainly comes from HCl in flue gas and process water. The Cl- content in process water is relatively small, so Cl- in slurry mainly comes from flue gas. When there is a large amount of Cl- in slurry, Cl- will be wrapped by crystals and combined with a certain amount of Ca2+ in slurry to form stable CaCl2, leaving a certain amount of water in the crystals. At the same time, a certain amount of CaCl2 in slurry will remain between gypsum crystals, blocking the channel of free water between crystals, causing the water content of gypsum to increase.
3. Influence of equipment operation status
1. Gypsum dehydration system Gypsum slurry is pumped to the gypsum cyclone for primary dehydration through the gypsum discharge pump. When the bottom flow slurry is concentrated to a solid content of about 50%, it flows to the vacuum belt conveyor for secondary dehydration. The main factors affecting the separation effect of the gypsum cyclone are the cyclone inlet pressure and the size of the sand settling nozzle. If the cyclone inlet pressure is too low, the solid-liquid separation effect will be poor, the bottom flow slurry will have less solid content, which will affect the dehydration effect of the gypsum and increase the water content; if the cyclone inlet pressure is too high, the separation effect will be better, but it will affect the classification efficiency of the cyclone and cause serious wear on the equipment. If the size of the sand settling nozzle is too large, it will also cause the bottom flow slurry to have less solid content and smaller particles, which will affect the dehydration effect of the vacuum belt conveyor.
Too high or too low vacuum will affect the gypsum dehydration effect. If the vacuum is too low, the ability to extract moisture from the gypsum will be reduced, and the gypsum dehydration effect will be worse; if the vacuum is too high, the gaps in the filter cloth may be blocked or the belt may deviate, which will also lead to worse gypsum dehydration effect. Under the same working conditions, the better the air permeability of the filter cloth, the better the gypsum dehydration effect; if the air permeability of the filter cloth is poor and the filter channel is blocked, the gypsum dehydration effect will be worse. The filter cake thickness also has a significant effect on gypsum dehydration. When the belt conveyor speed decreases, the filter cake thickness increases, and the vacuum pump's ability to extract the upper layer of the filter cake is weakened, resulting in an increase in the gypsum moisture content; when the belt conveyor speed increases, the filter cake thickness decreases, which is easy to cause local filter cake leakage, destroying the vacuum, and also causing an increase in the gypsum moisture content.
2. Abnormal operation of desulfurization wastewater treatment system or small wastewater treatment volume will affect the normal discharge of desulfurization wastewater. Under long-term operation, impurities such as smoke and dust will continue to enter the slurry, and heavy metals, Cl-, F-, Al-, etc. in the slurry will continue to enrich, resulting in the continuous deterioration of slurry quality, affecting the normal progress of desulfurization reaction, gypsum formation and dehydration. Taking Cl- in slurry as an example, the Cl- content in the slurry of the first-level absorption tower of the power plant is as high as 22000mg/L, and the Cl- content in gypsum reaches 0.37%. When the Cl- content in the slurry is about 4300mg/L, the dehydration effect of gypsum is better. As the chloride ion content increases, the dehydration effect of gypsum gradually deteriorates.
Control measures
1. Strengthen the combustion adjustment of boiler operation, reduce the impact of oil injection and stable combustion on the desulfurization system during the start-up and shutdown stage of the boiler or low-load operation, control the number of slurry circulation pumps put into operation, and reduce the pollution of unburned oil powder mixture to the slurry.
2. Considering the long-term stable operation and overall economy of the desulfurization system, strengthen the operation adjustment of the dust collector, adopt high parameter operation, and control the dust concentration at the dust collector outlet (desulfurization inlet) within the design value.
3. Real-time monitoring of slurry density (slurry density meter), oxidation air volume, absorption tower liquid level (radar level meter), slurry stirring device, etc. to ensure that the desulfurization reaction is carried out under normal conditions.
4. Strengthen the maintenance and adjustment of gypsum cyclone and vacuum belt conveyor, control the inlet pressure of gypsum cyclone and the vacuum degree of belt conveyor within a reasonable range, and regularly check the cyclone, sand settling nozzle and filter cloth to ensure that the equipment operates in the best condition.
5. Ensure the normal operation of the desulfurization wastewater treatment system, regularly discharge the desulfurization wastewater, and reduce the impurity content in the absorption tower slurry.
Conclusion
The difficulty of gypsum dehydration is a common problem in wet desulfurization equipment. There are many influencing factors, which require comprehensive analysis and adjustment from multiple aspects such as external media, reaction conditions and equipment operation status. Only by deeply understanding the desulfurization reaction mechanism and equipment operation characteristics and rationally controlling the main operating parameters of the system can the dehydration effect of desulfurized gypsum be guaranteed.
Post time: Feb-06-2025