Using a coal-fired power plant's flue gas desulfurization (FGD) system as an example, this analysis examines issues in traditional FGD wastewater systems, such as poor design and high equipment failure rates. Through multiple optimization and technical modifications, the solid content in the wastewater was reduced, ensuring normal system operation and lowering operational and maintenance costs. Practical solutions and recommendations were proposed, providing a solid foundation for achieving zero wastewater discharge in the future.
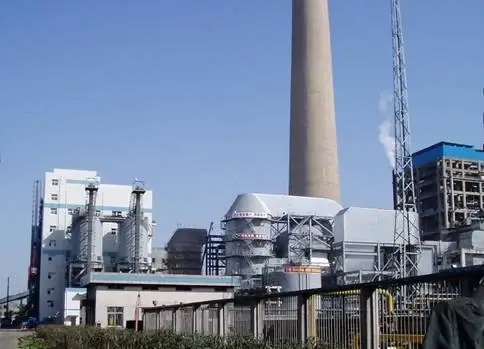
1. System Overview
Coal-fired power plants commonly employ the limestone-gypsum wet FGD process, which uses limestone (CaCO₃) as the absorbent. This process inevitably produces FGD wastewater. In this case, two wet FGD systems share one wastewater treatment unit. The wastewater source is the gypsum cyclone overflow, processed using traditional methods (triple-tank system) with a designed capacity of 22.8 t/h. Treated wastewater is pumped 6 km to a disposal site for dust suppression.
2. Major Issues in the Original System
The diaphragm of dosing pumps often leaked or failed, preventing continuous chemical dosing. High failure rates in plate-and-frame filter presses and sludge pumps increased labor demands and hampered sludge removal, slowing sedimentation in clarifiers.
Wastewater, originating from the gypsum cyclone overflow, had a density of approximately 1,040 kg/m³ with a solid content of 3.7%. This impaired the system’s ability to continuously discharge treated water and control harmful ion concentrations in the absorber.
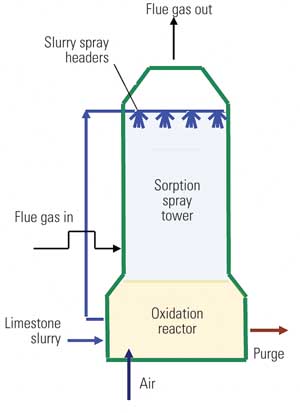
3. Preliminary Modifications
Improving Chemical Dosing:
Additional chemical tanks were installed atop the triple-tank system to ensure consistent dosing via gravity, controlled by an online concentration meter.
Result: Improved water quality, though sedimentation was still required. Daily discharge reduced to 200 m³, which was insufficient for stable operation of the two FGD systems. Dosing costs were high, averaging 12 CNY/ton.
Reusing Wastewater for Dust Suppression:
Pumps were installed at the clarifier bottom to redirect part of the wastewater to onsite ash silos for mixing and humidification.
Result: Reduced pressure on the disposal site but still resulted in high turbidity and non-compliance with discharge standards.
4. Current Optimization Measures
With stricter environmental regulations, further system optimization was necessary.
4.1 Chemical Adjustment and Continuous Operation
Maintained pH between 9–10 through increased chemical dosing:
Daily usage: lime (45 kg), coagulants (75 kg), and flocculants.
Ensured a discharge of 240 m³/day of clear water after intermittent system operation.
4.2 Repurposing the Emergency Slurry Tank
Dual-use of the emergency tank:
During downtime: Slurry storage.
During operation: Natural sedimentation for clear water extraction.
Optimization:
Added valves and piping at various tank levels to enable flexible operations.
Sedimented gypsum was returned to the system for dewatering or reuse.
4.3 System-wide Modifications
Lowered solids concentration in incoming wastewater by redirecting filtrate from vacuum belt dewatering systems to the wastewater buffer tank.
Enhanced sedimentation efficiency by shortening natural settling times through chemical dosing in emergency tanks.
5. Benefits of Optimization
Improved Capacity:
Continuous operation with a daily discharge of over 400 m³ of compliant wastewater.
Effective ion concentration control in the absorber.
Simplified Operations:
Eliminated the need for the plate-and-frame filter press.
Reduced labor for sludge handling.
Enhanced System Reliability:
Greater flexibility in wastewater processing schedules.
Higher equipment reliability.
Cost Savings:
Chemical usage reduced to lime (1.4 kg/t), coagulants (0.1 kg/t), and flocculants (0.23 kg/t).
Treatment cost lowered to 5.4 CNY/ton.
Annual savings of approximately 948,000 CNY in chemical costs.
Conclusion
The optimization of the FGD wastewater system resulted in significantly improved efficiency, reduced costs, and compliance with stricter environmental standards. These measures serve as a reference for similar systems seeking to achieve zero wastewater discharge and long-term sustainability.
Post time: Jan-21-2025